随着国内钢铁工业供给侧改革、产业结构调整、国标升级等政策的实施,线材行业向高品质、低能耗、绿色化发展的步伐不断加快。但长期以来受工艺技术及装备水平等影响,国内线材高速轧机装备技术在提高产品品质、降低轧制能耗及降低生产成本等方面进步缓慢。主要体现在:1)轧制能力小,不能适应低温轧制。2)轧机刚性差,产品尺寸波动大。3)受制于传统集中传动型式,工艺孔型设计及变形制度不灵活,轧机高速运行稳定性差,设备空载消耗及辊环消耗高。4)高速线材终轧机组速度高、结构复杂,对设计、制造和装配要求极高,创新开发难度极大,而进口装备费用高、供货周期长、备件及维护费用高,严重制约国内高速线材生产技术的进步与发展。针对高速线材行业转型升级存在的核心问题,本项目以高品质、低能耗及绿色化线材高速轧机装备技术为目标,创新性的提出了独立传动的模块化高速轧机装备技术理念,开发了全新的线材绿色、低耗独立传动式模块化高速轧机工艺、装备及控制技术,并实现了产业化应用,提高了线材生产的灵活性,提升了产品品质,降低了能耗及生产成本,实现了线材的绿色低耗生产。
图1 绿色低耗独立传动式高速线棒材模块轧机的研发技术路线
为解决高速线材行业所存在的痛点问题,中冶赛迪高速线材技术研发团队颠覆传统的集中传动技术思维,以独立传动的模块化高速线材生产技术为关键,通过对高速独立传动轧制过程金属变形、控轧控冷离线仿真、组织性能调控、模块化高速轧制装备及吐丝装备、自动化控制等关键技术的研究,创新开发出了全新的线材绿色、低耗独立传动式模块化高速轧机工艺、装备及控制技术,并实现了产业化应用。1、基于独立传动模块轧机,开发了高灵活性、高适应性的孔型系统,实现了对线棒高速轧制过程金属变形的精确控制;探明了高速线材轧制工序轧件传热特点,建立了轧制工序轧件换热模型,开发了控轧控冷离线仿真模型,实现了高速线材轧制工序温度仿真;开发了高速线材及高速棒材柔性化组织性能调控技术,实现了绿色低耗生产。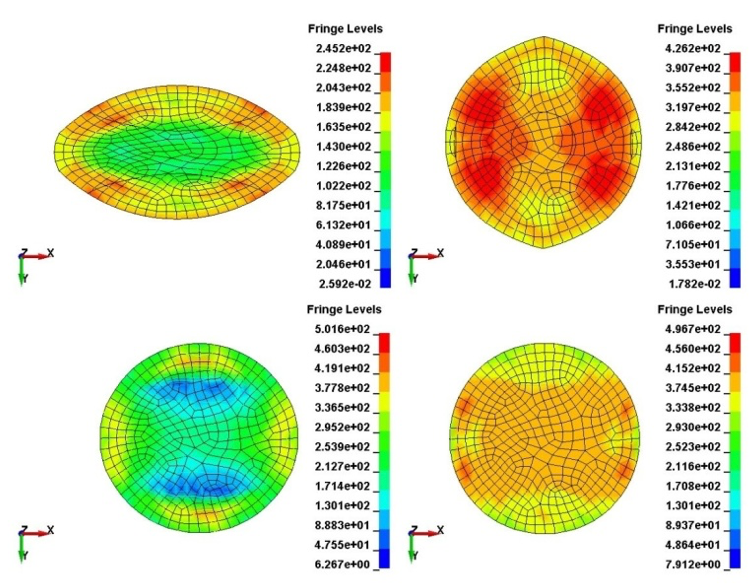
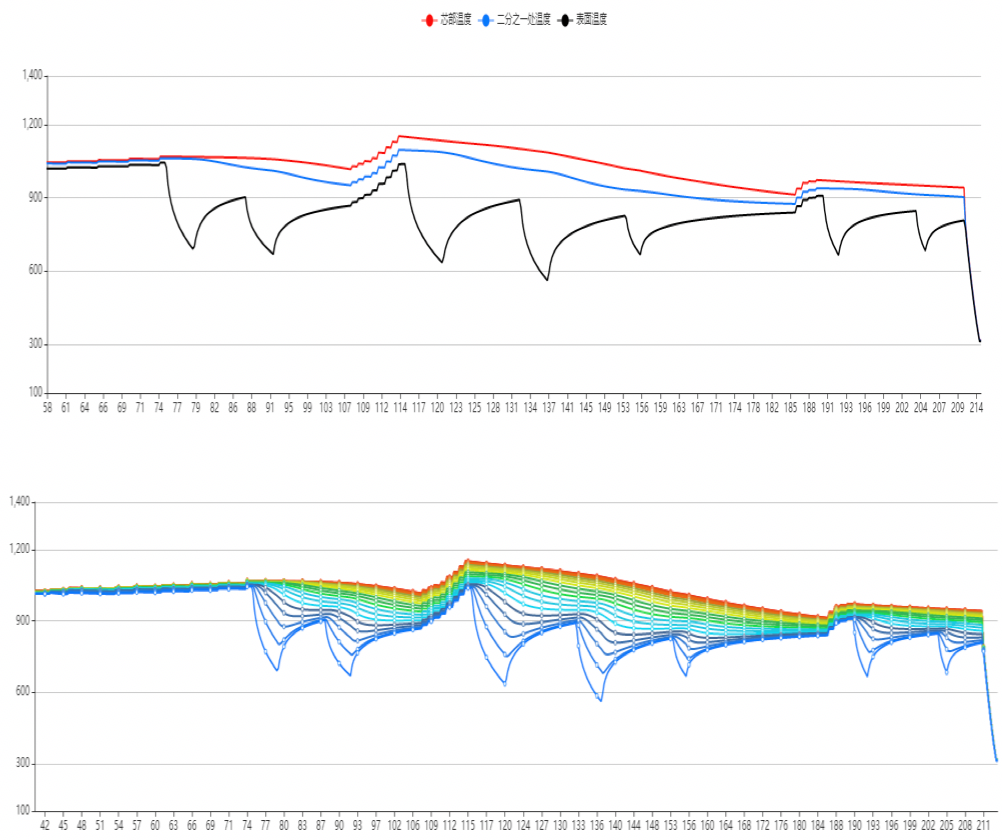
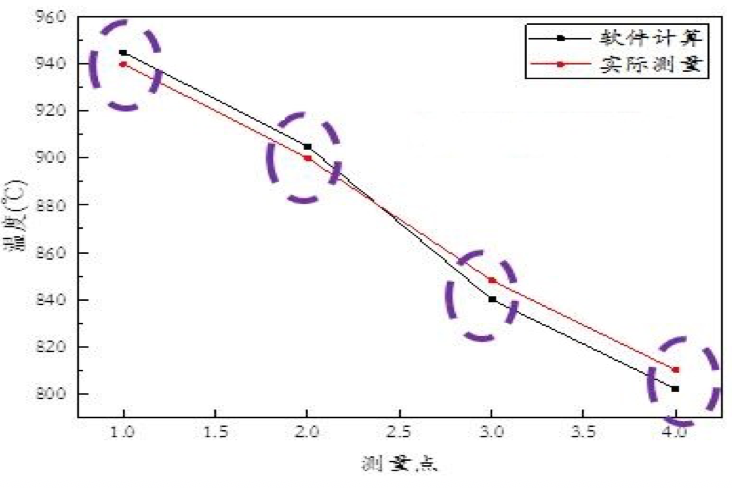
2、创新性提出了高速精轧机双模块化理念,开发出基于独立传动的模块化高速轧机,形成了具有高互换性及高适应性的超重载型250、230及高精度型150标准化轧机,实现了低温轧制及高精度轧制。开发了单一速比及多速比齿轮箱,与标准化模块轧机组合使用,实现了1拖1或1拖2的机组型式,缩短了传动链,简化了设备结构,提高了机组高速运行稳定性,消除了空载电耗,降低了辊环消耗。 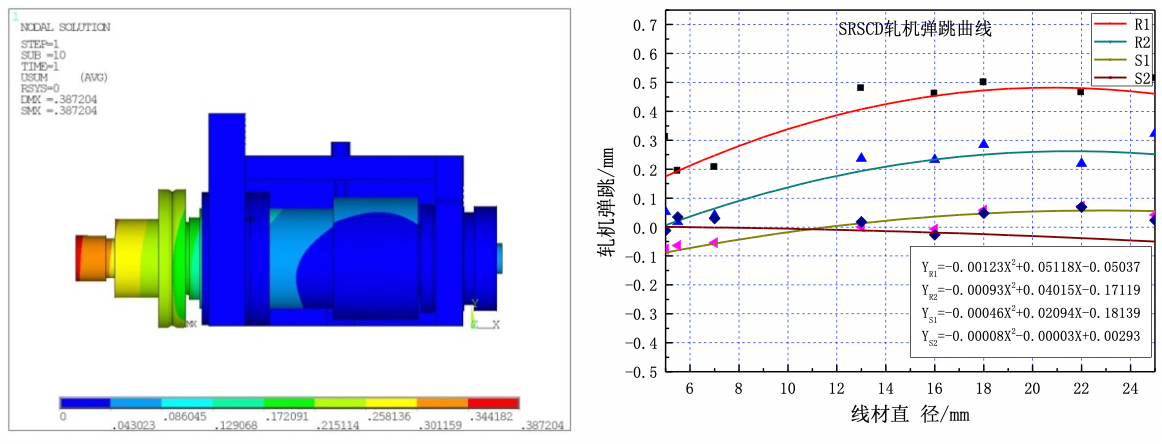

3、建立了吐丝管曲线力能模型,开发了曲率光滑的吐丝管曲线,降低了线材运行阻力;开发出吐丝头非对称转子动力学分析软件,实现了吐丝头轻量化设计,解决了吐丝头动平衡问题;采用阻尼减振装置降低了吐丝机的振动幅值。开发了120m/s的20度倾角吐丝机,可实现更大规格范围线材的低温高速吐丝成圈。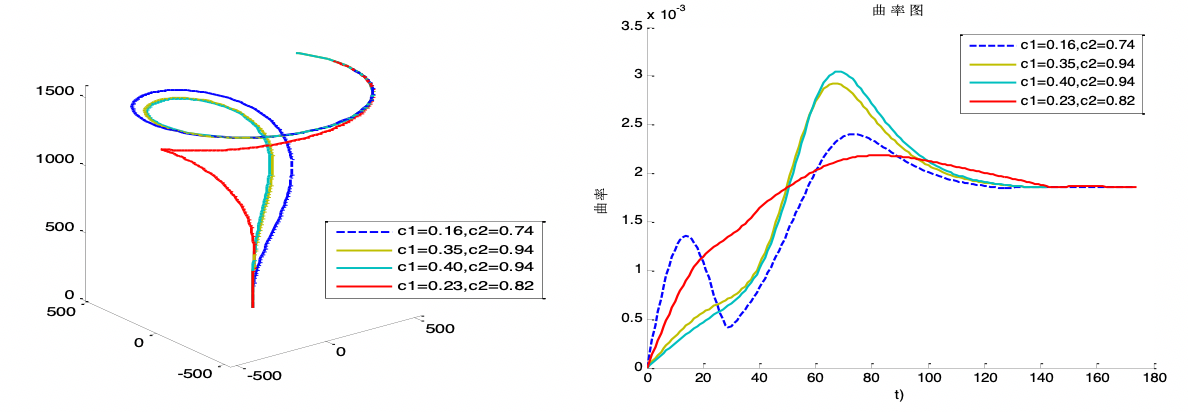
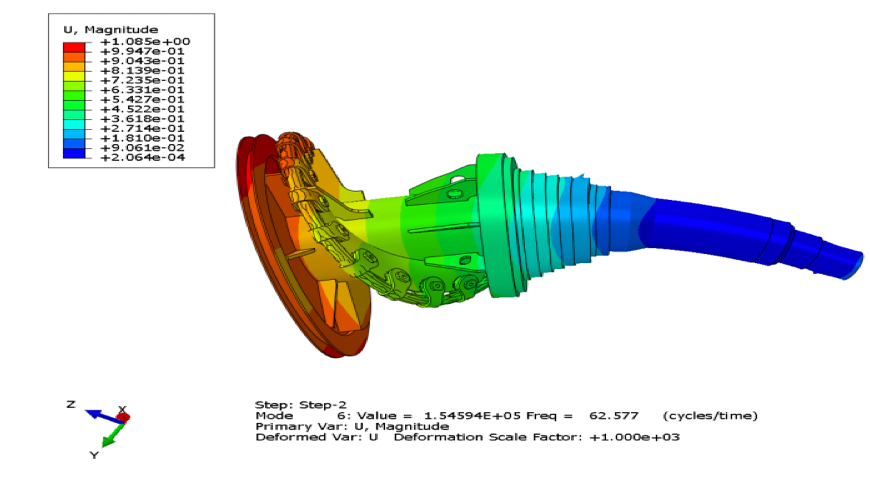
4、开发了自适应的动态速降补偿技术,消除了高速轧制过程中咬钢速降对轧制稳定性的影响;开发了多机架速度同步控制技术,替代了传统集中传动精轧机的机械同步,保证了高速稳定生产。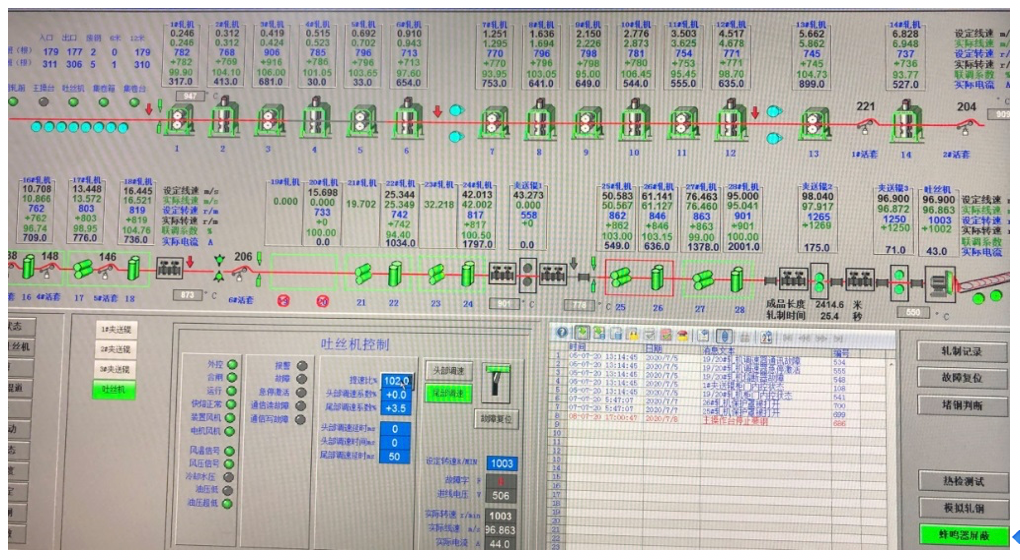
本项目创新技术已成功应用于江苏亚盛、福建三山、新疆天山及宁夏建龙等国内外30余家高速线材及高速棒材企业,产品累计销售近170台套。采用该技术实现了高速线棒材的低温轧制,HRB400E盘螺的锰合金含量降低20%,平均电耗较集中传动降低约5%,平均辊耗较集中传动精轧机降低约15%。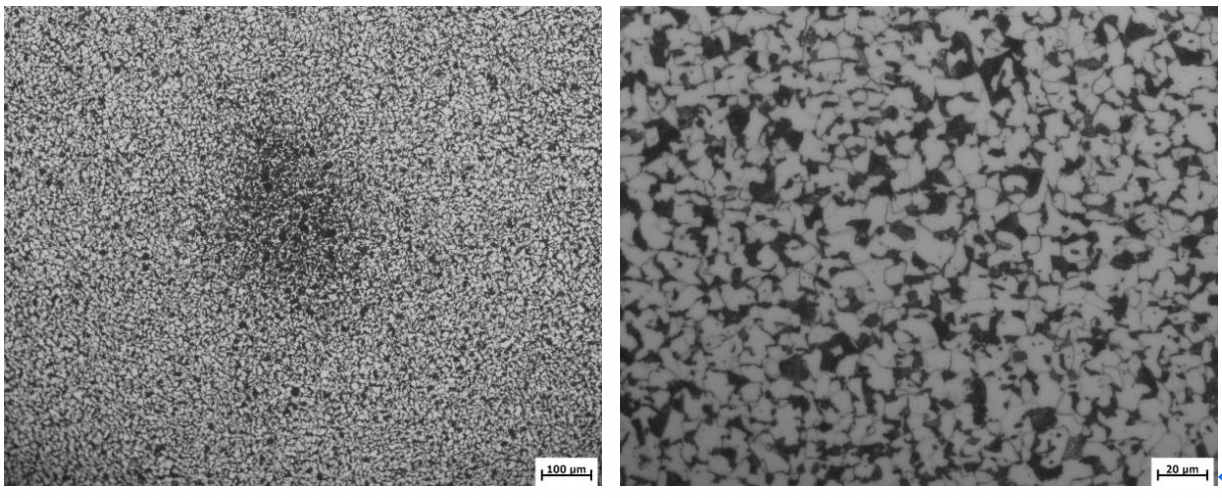
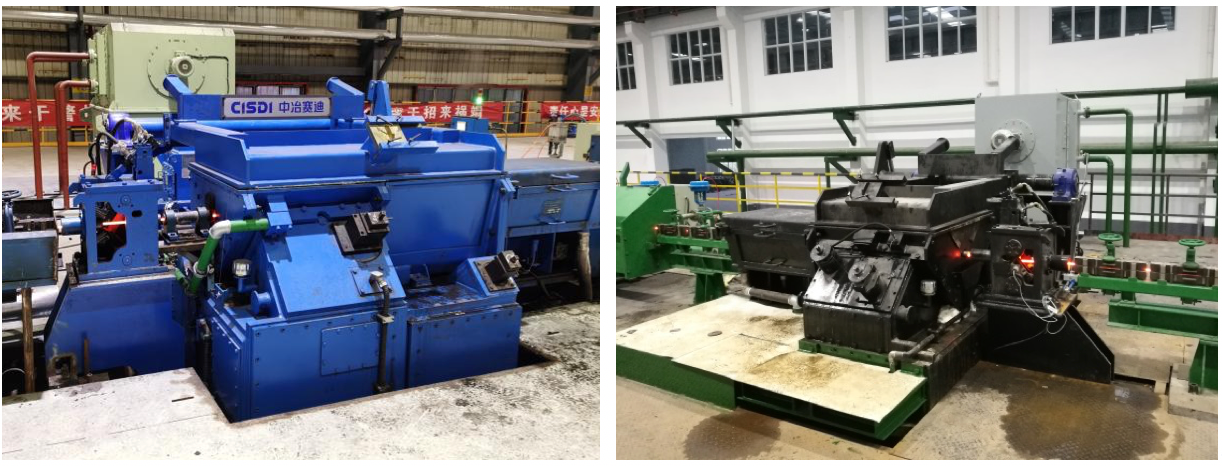
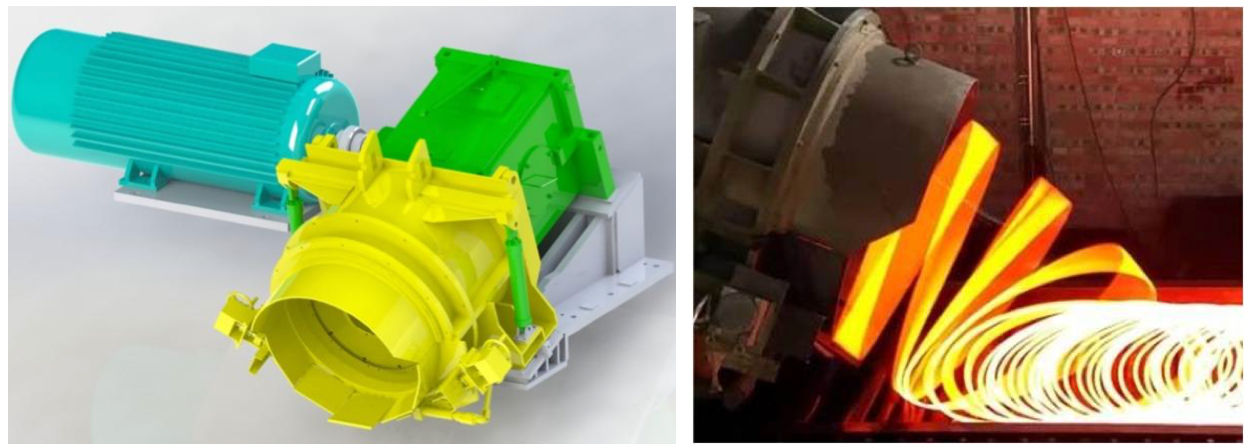
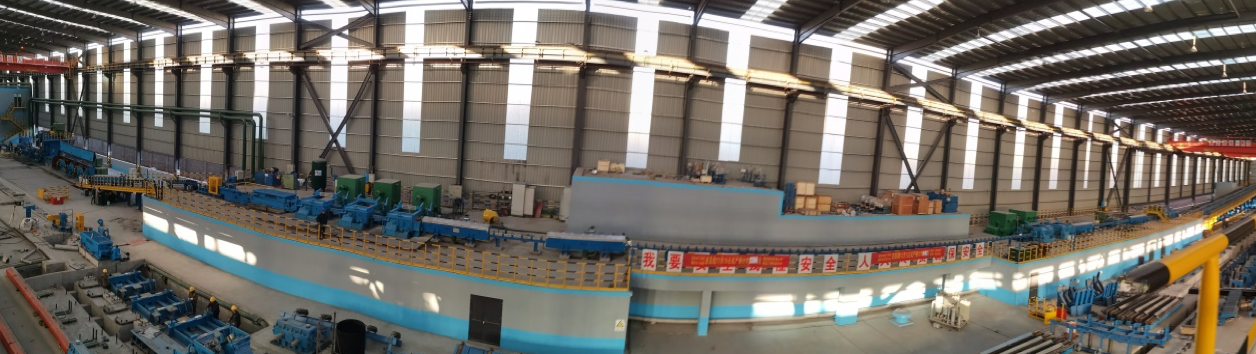
本项目成果已获授权专利28项,其中发明专利9项,申请专利PCT 3项,参编国家标准2项,发表论文10篇。经专家鉴定,本项目成果总体达到国际先进水平,其中开发的基于独立传动模块化轧机的高速线材柔性化组织性能调控技术达到国际领先水平。