徐春玲 张 惠 鲁继利 朱 建
(山东钢铁股份有限公司莱芜分公司炼铁厂)
摘 要 本文主要介绍了莱芜分公司炼铁厂265m2烧结系统为提高烧结矿FeO稳定性,分析流程可控因子,对燃料水分、燃料粒度、混匀料水分、四辊破碎质量、下料波动等进行了系列改善,试验分析、探测关键因子最佳控制水平,优化控制区间,使烧结矿FeO西格玛水平达到3.37,综合合格率98%以上。
关键词 烧结矿 焦粉 噪音因子 固定碳
1 前言
烧结矿的质量指标中,FeO含量是影响高炉炉况顺行的一个非常重要的参数,烧结矿FeO含量的波动区间越窄,烧结过程越稳定。在生产中适当降低烧结矿中的FeO含量,并提高其稳定性,既可以保证烧结矿的冷强度和低温还原粉化性能,又改善了烧结矿的还原性,使烧结矿的冶金性能得到改善,也有利于降低烧结固体燃耗、高炉焦比。莱芜分公司炼铁厂265m2烧结机,2018年烧结矿FeO为2.07西格玛水平且均值高达8.9%。为提高烧结矿稳定性,进而优化高炉炉料结构,提高高炉炉况稳定性,降低高炉炼铁燃料比和吨铁成本, 2019年立项攻关改进,改善后提升至3.37西格玛水平且均值降低0.46%。
2 关键影响因素分析
2.1 工艺流程分析
分析烧结工艺流程(见图1),流程不可控部分主要在于原铁矿粉、部分熔剂等原料的源头采购,经团队分析对流程影响程度后,流程可控度大于80%。
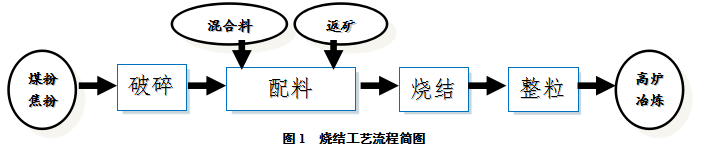
通过流程图分析得出可控因子9个:燃料水分波动、燃料大粒度多、燃料来料质量差、混匀料水分波动、烧结料面不平整、四辊破碎质量差、燃料配加人为判断不准、配料电子称误差反馈偏差、烧结终点温度控制不当。
2.2 部分因子快速改善
2.2.1 燃料水分波动
焦粉受料口无喷淋降尘设备,小焦筛区域除尘能力有限,上料容易造成扬尘。为降低焦粉扬尘,常采用水管直接喷洒焦粉方式。水管直接喷淋不均匀,用水量大,容易造成局部焦粉占水过湿。为此,增加雾化喷淋,卸焦粉时利用雾化喷淋降尘,避免焦粉扬尘,焦粉无明显润湿情况。(改善效果见图2)
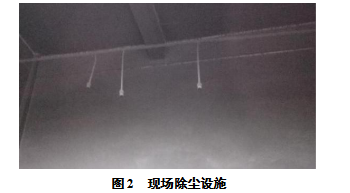
2.2.2 燃料大粒度多
烧结用焦粉来自焦化筛下焦粉、5、6号高炉槽下焦粉,燃料来源点多,焦粉经常混入大粒度焦块,增加烧结燃料破碎难度。造成原因有:高炉、焦化对焦粉筛维护不足,造成焦块混入;岗位人员清扫卫生、清除现场落料不规范,焦块混入焦粉;烧结区小焦筛磨损,造成大粒度焦块进入破碎工序。为此,年修期间对槽下小焦筛更换筛板,提高大块焦粉筛出率,避免大块焦粒进入四辊破碎。改进后燃料粒度趋于稳定,大粒度焦块明显减少(改进效果见图3)。
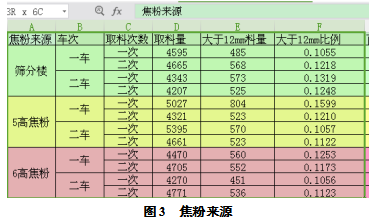
2.2.3 混匀料水分波动
混匀料水分受加水水压、返矿料温、白灰等因素影响,控制不稳定,造成烧结过程波动,影响烧结矿FeO稳定,且监督控制点全在一混,控制能力较低。在看火岗位增加水分自动控制监测装置,对水压、加水量、水分直接监测;制定可靠的水分控制标准,实现看火对水分的小范围直接控制调整,提高控制稳定性。
2.2.4 烧结料面不平整
烧结机泥辊下料口挡板磨损严重,造成料面布料不平整。利用检修期更换泥辊下料口挡板。烧结机六辊一根棍子损坏,减速箱内部齿轮有损坏,造成烧结料面布料呈波浪状,布料不平整。检修更换六辊设备(改善前后对比见图4)。
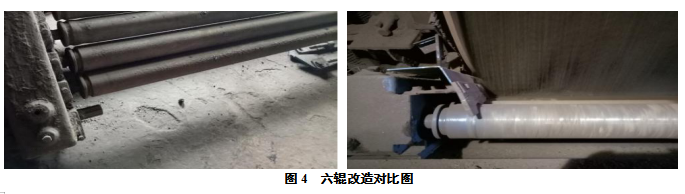
2.2.5 四辊破碎质量差
四辊维护不及时,维护人员中途更换,对车削质量把关不严。车削周期不固定、磨损量车削量标准不固定。为此,规范三台四辊破碎机循环使用,每周做一次定尺车削。规范四辊维护后,燃料破碎良好,燃料粒度3mm粒级保持80%以上。
2.3 其他因子实验分析
2.3.1 噪声因子
噪声因子来自四辊破碎燃料破碎质量、配料室、看火岗位操作人员水平差异,对烧结矿FeO的预知预控条件上不可改变,部分受控。经过方差分析,四个班组间操作无明显差异,FeO均值在8.32-8.55之间;但每班之间仍有轻微差异(见图5),丁班均值较低但标准差略高于其他班组,且四班内FeO波动仍很明显。因此,为进一步减少班组之间操作上的差异,除加强班组学习培训之外,借鉴防错法思想,制定统一操作标准,对影响操作的关键参数料批数通过控制图进行监控,并进行量化操作。
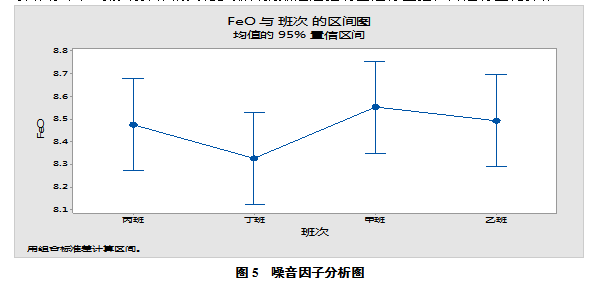
2.3.2 试验因子
配料下料误差与人为判断燃料配加量存在部分交互作用,需进行组合的检验;燃料质量细分为燃料粒度和固定碳。试验因子统计见表1。

建立回归方程,模型回归P值=0小于0.05(见图6),回归模型显著。其中:燃料粒度P0.869和终点温度P0.680均大于0.05,效果不显著,需逐步去除燃料粒度和终点温度后再做回归分析。去除燃料粒度建立回归方程模型回归P值=0小于0.05,回归模型显著,但其中终点温度P0.677均大于0.05,效果仍不显著(见图7);去除烧结终点温度建立回归方程,模型回归P值=0小于0.05,回归模型显著,但终点温度P0.877均大于0.05,效果仍不显著(见图8)。

同时去除燃料粒度、烧结终点温度,第四次建立回归方程为:烧结矿FeO% = -6.48 + 2.291 燃料配加量+ 0.0934 燃料固定碳含量%。模型回归P值=0小于0.05,各项P值也均小于0.05,回归模型显著(见图9);但R-sq71.33%、R-sq(调整)68.02% 水平仍较低。回归方程存在误差。考虑实际生产中,燃料粒度对烧结矿亚铁有较明显影响,仍考虑作为重要因子做进一步分析。烧结终点温度控制,技术要求较严格,生产中可通过减机速,降低布料等措施预防。可控性较高。
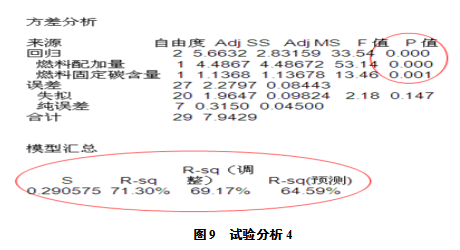
3 关键因子控制
3.1 最佳水平探测
选取1709批号料堆做最佳水平探测试验,燃料指标分析(燃料配加量2.8-3.3、燃料固定碳80-85%、燃料粒度74-82%),确认一元回归模型预测数据可靠,通过分析燃料配加量、燃料固定碳、燃料粒度参数,找出与烧结矿氧化亚铁对应关系。试验水平设定方案见表2。
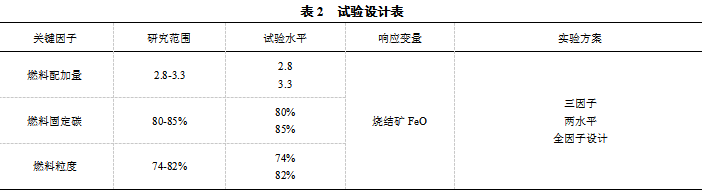
全因子分析结果:主效应P=0.000<0.05,说明模型总体有效;2.S=0.089,R-Sq=98.52%,R-Sq(调整)=96.75%,模型有效;燃料固定碳与燃料粒度二阶交作用显著,尽管燃料粒度主效应不显著,但仍须保留(见图10)。

通过曲面图和等值线分析得出:系统改进后,在满足烧结矿氧化亚铁8.0-8.6区间时,燃料量取值2.9-3.3、固定碳取值80.5-85%、燃料粒度74%-82%,满足可控制要求。
3.2 燃料下料量波动改善
燃破圆盘给料出料口盘面上积料、带料,严重时(大料流、物料粘湿或粒度细小等)盘面周边频繁撒料;且圆盘最大出料能力50%达不到25t/h,达不到工艺标准要求值。为此,借鉴同行业经验,在盘面焊接0.5m钢筋;出料口长宽扩大,上边角弧度光滑。改进后圆盘最大出料能力100%达到35t/h,且出料口盘面上出料顺畅,无积料、带料,盘面周边无撒料现象。原配料7#、8#使用时间较长,维护调整不及时,设定电子称量程1.5-5.0,下料量波动幅度大,实际下料误差在10%以上,远远超出工艺要求4%。对配料7#、8#仓电子称更换,更换原频率调整燃料下料量方式,采取重量设定方式,下料准确,平均误差控制在3%以内。
4 改进效果
4.1 烧结矿FeO
最佳效果显著性验证:取改善前(5月)和改善后(10月)的数据,进行双样本T检验(样本量85)。统计结论:烧结矿FeO均值降低0.46 (见图12),质量波动明显降低。
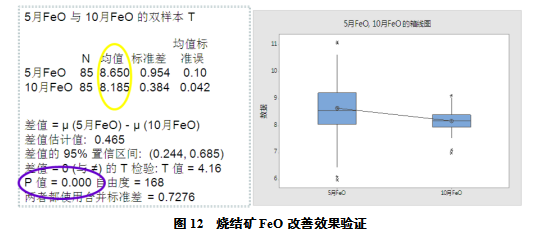
4.2 烧结矿低温还原粉化率
取改善前(5月)和改善后(10月)烧结矿低温还原粉化率数据,进行双样本T检验(样本量31)。统计结论:改善前后对比烧结矿低温还原粉化率差异不大,烧结矿FeO适当降低,未对低温还原粉化率造成影响(见图13)。
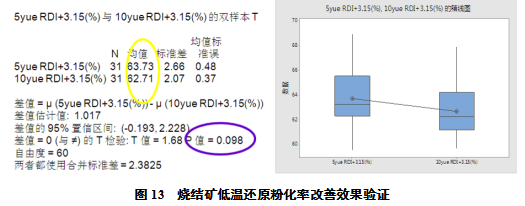
5 结论
烧结矿FeO质量稳定,可有效减少高炉炉况波动,保证高炉生产稳定。原生产操作仅追求烧结矿FeO合格率,未对烧结矿质量稳定做有效控制,造成烧结矿FeO存在较大波动。经过项目团队系列改进实施,主要通过对烧结燃料粒度有效控制、固化燃料调整等措施,加强烧结过程控制,提高烧结矿成分稳定性。烧结矿FeO西格玛水平达到3.37,综合合格率98%以上,超额完成预期目标,对同行业具有加大的推广价值。