
低碳绿色炼铁技术发展动态及展望
刘然,张智峰,刘小杰,李欣,李宏扬,吕庆
(华北理工大学冶金与能源学院, 河北 唐山 063210)
摘要: 当前,为积极应对气候变化等一系列问题,世界各国纷纷提出了绿色减排计划。与此同时,中国相应提出了“碳达峰、碳中和”节能减排目标,并以“1+N”等政策体系作为实现可持续发展战略、积极应对气候变化、履行大国义务的核心支持。钢铁工业作为31个制造业门类中碳排放量最大的行业,自然而然成为节能减排战役中的“排头兵”。目前,复杂的高炉生产工艺仍然以煤、焦等化石资源作为主要燃料,使得其成为钢铁流程中的碳耗大户、碳排放大户、污染排放大户,因此高炉炼铁工艺的绿色低碳转型升级已迫在眉睫。从背景介绍、发展动态以及未来发展展望这3大部分对低碳绿色炼铁技术进行论述,其中对绿色低碳炼铁技术发展动态部分进行了详细阐述。首先就优化节能低碳操作和构建循环经济环保圈两个层面,从精细炉料操作、提升生产技术等多个角度讨论了如何实现高炉工艺低碳绿色炼铁;其次从非高炉领域入手,对直接还原工艺和熔融还原工艺的国内外发展现状进行阐述,并进行了相应的比较与分类汇总;之后从创新型炼铁工艺(氢冶金、智能化炼铁)角度探讨了此类技术的发展态势。最后,综合当前绿色低碳炼铁技术发展最新动态进行了5个方面的展望,明确了“绿色低碳为方向,节能减排是目标”的任务方向。
关键词: 炼铁技术;氢冶金;温室效应;绿色低碳;节能减排
现今,“碳达峰”、“碳中和”已经成为焦点话题,两者更是2021年的两会热词。“碳达峰”要求中国在2030年前实现煤炭、石油、天然气等化石能源燃烧活动以及工业生产等方面产生的CO2不再增长;“碳中和”则为通过节能减排、种植绿植等手段抵消某段时间产生的CO2排放量或温室气体总量,实现零排放。究其由来,主要是由于气候变化、资源枯竭等问题已严重威胁人类生命系统,世界各国纷纷出台绿色经济计划来进行节能降碳,在此背景下中国遂提出“碳达峰”、“碳中和”目标。该目标是由国家主席习近平于2020年在第75届联合国大会上首次提出,其既是实现中国可持续发展、加强生态文明建设、实现美丽新中国目标的重要抓手,又是面对严峻气候变化,中国履行大国责任、推动构建人类命运共同体的责任担当。《2030年前碳达峰行动方案》明确提出,通过绿色能源低碳转型行动、节能降碳增效行动、工业领域碳达峰行动等10个行动实现碳减排。根据IPCC(Intergovernmental Panel on Climate Change)公布的《2006年国家温室气体排放清单指南》(图1)可明显看出,钢铁行业作为化石能源消耗大户、碳排放大户必然成为碳减排的主要目标,同时,钢铁行业实现碳减排既是积极应对气候变化的重要举措,又是可持续发展的重要挑战。由于中国粗钢产量占全球产量的1/2以上,加上生产工艺主要以“高炉-转炉”为主,从而导致中国钢铁行业碳排放量占全球钢铁碳排放总量的60%以上,占全国碳排放总量的15%左右,是31个制造业门类中碳排放量最大的行业。燃料燃烧对CO2排放量的贡献量和钢铁工业各工序CO2排放占比如图2和图3所示,通过对比不难发现,钢铁长流程工艺体系中炼铁工艺CO2排放量占80%左右,以煤、焦炭等长期占据主导地位的高炉部分CO2的排放量占比高达73.6%,远超烧结、炼钢等工艺。所以发展绿色低碳的炼铁技术对降低钢铁行业碳排量、发展低碳钢铁新格局尤为重要。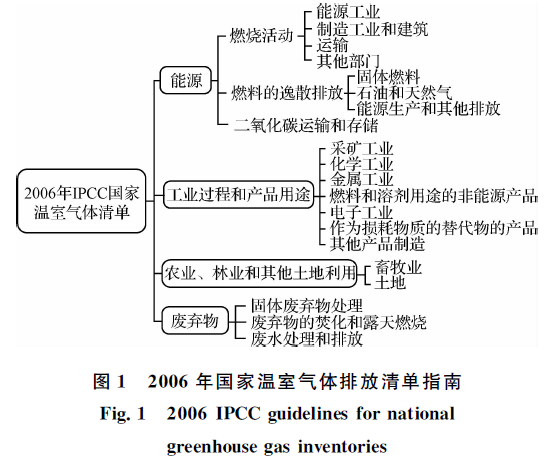
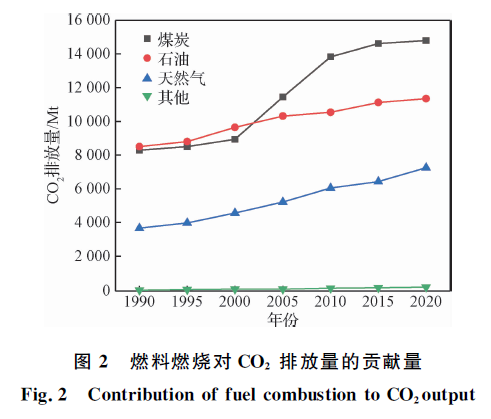
传统的炼铁工序为“炼焦→烧结→高炉”。在这一流程中,各个环节都有可能成为碳排放和大气污染的关键源,具体而言:原燃料等装卸运输过程中会产生粉尘污染;焦化过程会造成二英等污染物的排放;烧结过程产生的烧结废气、粉尘、硫化物以及氮化物等易造成大气污染;而高炉作为消耗焦煤的主要场所,其产物除铁水外还伴有炉渣、SOx、CO、CO2等固废和气体的产生,极易成为温室气体排放源和大气污染源。综上所述,除原燃料运输外均会产生能耗(表1),因此,炼铁技术低碳绿色化程度直接影响整个钢铁流程节能减排效果。
2.1优化节能低碳操作
随着能源消耗,钢铁企业开始面临富矿减少、品位下降、选矿难的局面,加上成本问题导致低成本矿石滥行,出现“劣矿驱逐优矿”的恶态,导致高炉燃料比上升,极易造成能耗增加、污染更加严重的局面。所以,实现炼铁工艺节能减碳首先应从燃料比这一角度出发,寻求降低高炉燃料比的技术措施,通过降低燃料比达到低碳冶炼的效果,探索符合新时代的绿色低碳炼铁技术。做好精料工作是降低燃料比、实现低碳冶炼的基础。传统高炉炉料主要通过烧结矿与球团矿各占一定比例来保证生产,其中烧结矿占比较大。然而研究表明,烧结过程耗能与污染物排放量均高于造球过程。鉴于这种情况,烧结工序要想实现低碳绿色化,有两个方面的改进措施可以选择:一方面,发展先进的烧结工艺,在一定程度上降低污染物的排放;另一方面,增加高炉球团矿比例以代替烧结矿。如首钢京唐对550 m2烧结机采用烧结料面喷吹蒸汽技术进行生产,不仅改善了烧结料层的传热制度,而且实现了烧结过程二英、NOx、CO的协同减排;河钢通过在高炉中使用高比例球团的试验研究发现,其具有提升经济效益、降低焦比和燃料比的积极效果。除此之外,还可效仿日本新日铁将碳与含铁原料混合制粒后,采用含碳球团矿来精化炉料,降低高炉热储备温度,提升高炉料的还原效率,达到节能减排的效果。提高风温也是降低燃料比的重要措施之一。综合国内外技术指标,日本、芬兰等地的先进高炉平均风温达到1 300 ℃左右,而中国仅为1 150 ℃左右。热风炉作为炼铁工序中最重要的送风设备,却由于高炉煤气低热值的特点限制了热风炉温度。所以,实现低热值高炉煤气全燃烧是直接提高高炉风温的一项突破性技术。首钢京唐等对5 000 m3巨型高炉采用顶燃式热风炉与高温空气预热耦合工艺,通过调控拱顶温度,不仅能实现低热值煤气全部燃烧,而且在保证NOx排放量的前提下使风温能达到1 250 ℃以上。当然,目前出现的节能减排措施并不仅局限于上述所提到的,还可通过喷吹技术、提高顶压等技术手段降低高炉燃料比。近年来,高炉喷吹生物质成为一个热门话题,为避免传统高炉炼铁工艺燃烧化石能源造成大量CO2排放到空气中,有不少学者开始将生物质运用于高炉喷吹,并就其可行性、研究现状等进行了分析。而喷吹塑料、喷吹焦炉煤气等手段则已经开始工业化应用,如德国、日本和奥地利已使用风口喷吹塑料技术的高炉,喷吹率高达60~80 kg/t;国内的鞍钢、济钢、莱钢等通过高炉喷吹焦炉煤气技术、提高顶压技术实现了碳减排,降低了燃料比。2.2构建循环经济环保圈
当前,由于中国钢铁产能过剩及产能削减政策的出台,市场上出现大量的废钢。利用废钢作为部分高炉原料不仅可以提升高炉透气性、降低燃料比、提高铁产量、实现低碳绿色化炼铁,还能为电炉和转炉分担部分压力。国外废钢入高炉工艺使用已久,北美钢铁企业对该技术的应用范围最广,其25座高炉中已有23座使用废钢等金属材料作为高炉炉料,废料使用率高达213 kg/t。研究表明,废料入炉率的增加使得高炉炉温明显升高,进而达到降低燃料比的效果。此外,中国韶钢、安钢、柳钢等高炉通过配加废钢工艺,在提升经济效益的基础上,改善了高炉透气性,降低了燃料比,大大降低了冶炼用焦量和温室气体的排放量。因此,通过提高资源利用率的同时减少炼铁工序的能耗也是一种低碳绿色炼铁的方式。高炉煤气作为高炉冶炼的主要副产品,其中以硫化物及酸性气体形式存在的氢、氯、氟等易造成污染。积极响应《关于推进实施钢铁行业超低排放的意见》等号召,秉承可持续发展、降低能耗、节约资源等理念,提高对高炉煤气有效利用,完善煤气回收利用技术,是未来企业炼铁工艺实现绿色低碳发展的必要手段。现阶段高炉煤气利用方式主要有直接作为热风炉、炼焦炉等工序燃料;回收高炉煤气余压余热进行发电;生产化工产品等。实践表明,宝钢采用TRT透平发电机组利用煤气压力能和热能发电,使高炉工序能耗回收率高达65%,实现了节能降耗。此外,通过对高炉煤气中的CO2、CO分别进行提质利用,不仅可起到节能减排的效果,而且还能生产制备工业所需化工产品,契合了当前国内外炼铁技术绿色低碳化的发展方向。然而,高炉炼铁工艺中除上述所提到的以外,高炉水渣、热风炉余热、烧结烟气等也可成为回收再利用目标。近年来,钢铁行业开始推广碳捕获利用与封存技术,从排放源头入手直接切断碳排放源,从而提高资源利用率、减少碳排放。如日本COURSE50计划利用碳捕获技术对高炉煤气CO2分离;韩国 POSCO所研究的碳捕获技术目前对体积分数大于95%的CO2的有效捕获率可达90%以上,CO2的日常捕获能力达到10 t左右。但由于成本、能耗等问题的限制使得该技术在钢铁行业的应用还处于探索阶段。虽然碳捕获相关技术支持所花费成本较多,但从长远来看却保证了企业经济效益,可实现节能减排。2.3非高炉炼铁技术
焦炭是高炉冶炼不可或缺的原料之一。然而,面对焦煤资源有限、大气污染严重等问题及可持续发展观念日益提升的现状,为提高节能减排效率,高炉炼铁技术逐渐受到各种限制,非高炉炼铁技术开始迅速发展。相比于传统的高炉炼铁技术,非高炉炼铁技术提倡以非焦煤为主要能源,大大提升了环保水平,并且还省去烧结造块工序,打破了传统炼铁技术的“长流程”限制。对现阶段主要炼铁工艺设计能力和能耗比较不难发现,现阶段非高炉炼铁技术以其节能、低成本、环保等特点成为各国炼铁工艺发展的焦点。主要炼铁工艺设计能力和能耗比较见表2。
非高炉炼铁技术分为直接还原工艺和熔融还原工艺两类。直接还原工艺不依赖于焦炭,省去了炼焦设备,并且还可得到高品位铁精矿。同时,按照还原剂的不同可将其分为气基和煤基两大类。气基直接还原技术主要有MIDREX工艺、HYL-III工艺、FINMET工艺;煤基直接还原技术主要有Fastmat工艺、ITmk3工艺、SL/RN工艺,目前均已投入工业应用。据世界DRI统计数据显示,受新冠疫情的影响,2020年世界直接还原铁产量为1.044亿t,比2019年同比下降了3.4%,这表明直接还原炼铁技术在近几年内备受青睐,但其中MIDREX与HIY-III工艺仍然占主导地位,所以在保持现有技术的基础上还需加大对其他工艺的研究。熔融还原工艺是将天然块矿、球团或粉矿在高温条件下用碳进行还原得到熔融态金属铁。目前投入工业化生产的主要有COREX、FINEX、HIsmelt以及CISP这4类工艺。和传统高炉相比较,熔融还原工艺主要将煤作为燃料,几乎不需要冶金焦炭,因其低成本、低能耗、低碳、低排放等特点,使其在非高炉领域得到很大的发展。实践表明,宝钢引入COREX工艺后,经过自主创新的八钢欧冶炉已经成为中国绿色低碳炼铁的代表,其实际工序能耗低于设计能耗,再配合其他技术升级,完全可以达到或优于炼铁工序能耗清洁生产的一级标准(HJ/T 427—2008)中能耗不超过385 kg/t(铁)的指标;FINEX工艺成功将流化床反应系统商业化,有效解决了资源、副产品的回收、有害物的排放等问题,并且SOx和NOx排放水平比预期降低了20%~50%;山东墨龙于2012年成功将HIsmelt工艺用于连续工业生产,不仅成功吻合了力拓在试验中所发现的铁水产量和煤耗的相关关系,而且能够使SOx排放量降低90%以上,大大提升了能源利用效率和环保效益;建龙集团CISP工艺工业化运行后,SO2和NOx排放量减少38%,粉尘排放量减少89%,并且无二英和酚氰废水排放,此外,还实现了CO2排放量减少11.2万t/a。2.4创新绿色低碳炼铁技术
2.4.1氢冶金技术
为摆脱对化石能源的依赖,炼铁技术的发展将目光聚焦于氢能。作为21世纪最具有发展力的能源,其绿色低碳、来源广、热值高等特点吸引了诸多国家就其在冶金领域的利用展开研究。在国外,有欧洲ULCOS的“氢”子项目、日本富氢还原铁矿石的“COURSE50计划”、韩国POSCO氢还原炼铁工艺、奥地利“H2FUTURE”绿色氢气存储技术、德国蒂森克虏伯氢基炼铁试验等。在国内,宝武集团作为中国钢铁行业氢冶金的先锋队,早在2016年就开始筹划氢冶金绿色低碳炼铁项目,主要从富氢碳循环高炉工艺、以氢代碳还原工艺等方面入手,并在新疆、湛江等地筹建了氢冶金创新基地,随后与中核集团、清华大学联手开发“核能制氢”技术;河钢宣钢启动建设规模为120万t的氢冶金示范工程,采用零重整技术替代传统碳冶金;中晋太行已经开始使用氢基直接还原铁工艺,且形成了具有自主知识产权的CSDRI气基竖炉还原铁技术;此外,鞍钢、包钢、建龙以及一些其他科研院所等也展开了氢冶金技术研究,均取得理想效果,降低了碳排放,找到了适合各企业特有的氢冶金低碳炼铁技术。国内外氢冶金主要研究现状及目标见表3。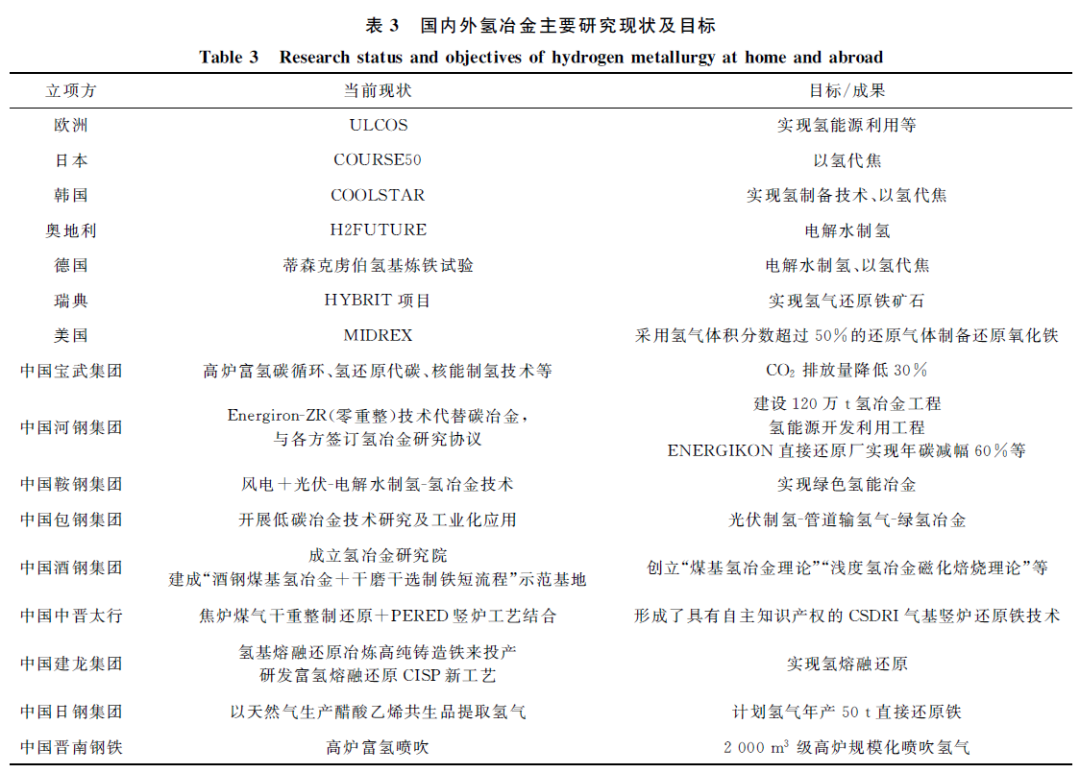
2.4.2智能化炼铁技术
智能化是炼铁工艺提高节能减排效率、实现环保的重要手段。2021年11月15日国家发展改革委员会发言人孟玮明确表示,目前工业等领域实施方案和《科技支撑碳达峰碳中和行动方案》已经编制完成,后续将按程序印发实施,这一消息无疑是当前智能化炼铁工艺技术发展的强心剂。当前“德国工业4.0”与“中国制造2025”的融合,以及节能减排、“双碳”等意见的出台,无不表明现阶段炼铁工艺流程向智能化、信息化、数字化融合发展已然是大势所趋。传统高炉由于自身特性的限制,因其冶炼强度高、数据量多、流程长、信息时滞性高、黑箱化严重等特点,其潜力未能被挖掘出来,容易导致大污染、大能耗的结果。新时代炼铁工艺应积极融合5G技术,加速工艺互联网平台的建设,利用大数据挖掘技术、机器学习技术、人工智能技术等对传统炼铁工艺流程进行“点对点”跟踪式监测,达到实时分析预测、及时科学决策的效果。研究表明,越来越多的企业、科研院所及高校等的学者都开始探究智能化在冶金中的应用。宝武集团以“力争2025年具备减碳30%的工艺技术,2035年力争减碳30%”为目标,目前正在建立智慧型炼焦、智慧型烧结、智慧型高炉三位一体智能炼铁工序,其中智慧型烧结目前已建成1、2烧结,对在建的3烧结中首次采用混合料水分和粒度监测机器人系统、烧结过程水-碳-风关键要素智能控制模型与系统等,力争实现固体燃料单耗小于40 kg/t;智慧型高炉汇集了上海宝山、武汉青山、南京梅山、湛江东山4大基地的炼铁工序,运用“互联网+”、大数据等技术实现了高炉炉况指数化诊断、高炉运行智能控制、高炉指标全面化对标等模块,尤其是高炉闭环控制更是实现了经济技术指标、成本、工序能耗对标等功能的应用,开启了数字高炉新时代。此外,宝钢自主研发的高炉智能专家系统投产运行后,吨铁燃料比下降近3.7 kg/t,铁水一级品率提升了5%,达到了稳定炉况、降低辅助燃料消耗、改善铁水质量的效果;马钢2号高炉采用的热风炉智能化控制系统经实际生产表明,燃烧状态明显得到改善,煤气消耗量显著降低,大大提升了经济效益;酒钢融合大数据技术、物联网技术等建立的专家机理模型,不仅能够实现对炉况的模型监控和生产指导,而且通过建立合理有效的预警机制实现了高炉安全长寿,有效降低了吨铁燃料比的同时提升了经济、社会效益。另外,首钢、包钢等也都打造了属于自己的智能化炼铁工艺流程。以上均为钢铁企业在炼铁智能化发展过程中的一些成果,而研究院、高校等相关专业人员也做了许多贡献。沙钢研究院建立的炼铁工艺大数据平台,可实现原料质量预警、故障预警、高炉炉况诊断等功能,不仅操作简单,方便操作人员对工艺流程进行实施监督,而且还能够及时对工序操作进行调整,其具体框架如图4所示;赵宏博等提出的炼铁大数据平台更是契合了《工业和信息化部关于印发钢铁工业调整升级规划(2016—2020年)的通知》中发展智能制造主题思想,该设计构建了一个完整的炼铁生态圈,充分实现了数据共享,更是融合了钢铁企业、科研院所及高校等不同层次的角色,能够达到集思广益、共同促进中国炼铁工艺发展的效果。
节能减排提出以来,绿色低碳炼铁技术刚性发展,智能化转型势在必行。然而,智能化在炼铁技术革新过程的应用中需要解决的问题还有很多,难度也越来越大,应加强与科技板块合作,走“工艺流程为主,计算机技术为辅”的路线,切实解决炼铁工艺数据存在的问题,实现节能减排绿色发展的目标。
钢铁行业作为国民经济的中流砥柱,是国家经济水平和综合国力的重要标志。而炼铁工艺作为钢铁流程的“高耗能、高排放”大户,其绿色低碳化程度足以彰显钢铁行业节能减排水平。“绿色低碳为方向,节能减排是目标”已然成为如今绿色低碳炼铁技术发展的必由之路,然而,中国低碳绿色炼铁技术的发展急不得,也慢不得。21世纪的今天,应该以“着眼当前,展望未来”的眼光去看待绿色低碳炼铁技术的发展。(1)以节能减排为目标,工艺改革为手段,不断探索传统高炉工艺低碳技术。通过发展精细炼铁原料、优化高炉操作等基础技术,提高高炉煤气、焦炉煤气、炉尘等副产品循环利用技术,增强喷吹生物质、碳捕获利用与封存等创新技术来达到节能减排的目的。此外,还可结合自身实际来完成工艺“长流程”向“短流程”转变。(2)大力发展非高炉和氢冶金技术,优化能源结构和流程结构。以科学技术为手段,提升“非高炉-电炉”协同减排能力,发展低成本制氢技术,摆脱对焦炭等化石能源的依赖,实现成熟的商业化低碳炼铁生产模式。(3)积极与两化(智能化、信息化)相融合。以5G、大数据技术等手段作为发力点,使用智能监控手段对炼铁流程各部分监测,实现在线预警、数据收集等功能,用科技创新助力炼铁技术向着绿色低碳化发展。(4)制定统一标准。当前世界各国作为“命运共同体”的一部分,碳排放标准、污染物排放标准、能耗标准等标准不一样,势必会出现“一国影响他国”的局面。(5)坚持“引进来、走出去”,积极参与国际间交流合作。有能力的钢铁企业应当积极引领国际低碳技术研发等活动,充分利用全球低碳炼铁生态圈优势资源,加强创新技术研究,为实现中国“30·60”目标贡献一份力量,为实现全球节能减排贡献一份力量。