根据预测,未来30年,石油需求将呈现下降趋势,以太阳能为首的可再生能源将成为增长最为迅速的能源。随着习近平总书记提出“碳达峰、碳中和”战略目标,并将之列为未来重点任务之一,我国光伏发电技术步入新时代。在光伏产业新时代背景下,“降本提效”成为主体趋势。光伏组件作为光伏发电的核心部件,是降低光伏成本,提高发电效率的基础。因此,研发低成本、高效率的光伏组件是光伏产业不断发展的必由之路。随着光伏研发人员和生产企业对光伏组件“降本提效”技术的不断探索,高效光伏组件层出不穷。
罗学涛、牛海燕团队结合光伏组件发展现状,对各项组件新技术的生产制备、可靠性性能、输出性能进行了详细研究,并结合产线设备、实验室分析仪器与计算机模拟,从微观分析、数据模拟以及仪器测试等方面给予了较为全面的分析。下面,本文对各项组件新技术的研究成果进行总结。
栅线在电池中起到收集和汇流电流的作用,但会形成一定遮挡面积从而影响电池效率。无主栅技术的本质是通过优化电池片电极、焊条和组件来提效降本。该项技术具有三大显著优势:一是降低电池片材料成本,二是降低遮光面积,三是提升电池片的电流收集能力。
焊接型无主栅组件技术仅改造焊接设备,即不改变电池片结构及组件制作工艺。对于此类组件技术,应重点关注焊接稳定性和组件失效机理,即焊接时电池片的失效、组件湿热老化过程中的失效、组件热循环过程中的失效。
罗学涛、牛海燕团队于实验分析并结合组件制作水平,设计出一款符合现阶段发展现状的无主栅焊接型组件,针对此类型组件的稳定性和失效机理展开了深入研究,其所用材料和结构为:多晶硅电池片基底、正面电极、四段背面电极、矩形截面焊条、双玻组件结构。主要成果如下:
晶硅电池片在焊接过程的主要失效形式是裂纹和虚焊,裂纹发生的比率远高于虚焊,并且裂纹对电池片或组件存在长期影响。在焊接过程中,电池片受到外部机械力或内应力,继而在电池片中产生裂纹。其中有些裂纹存在于银电极、Sn37Pb合金及背铝层中,当吸收足够的能量,将有可能扩展至电池片内部,导致电池片破裂。
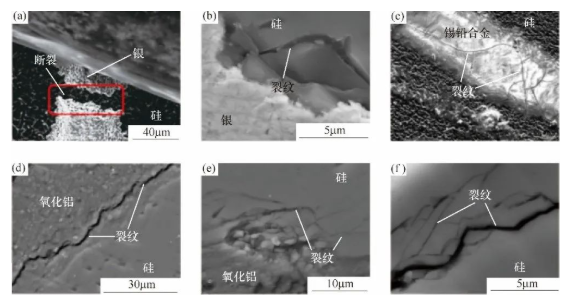
焊接过程中电池片中材料产生的裂纹缺陷
(a)银电极的断口;(b)依附于银电极的硅片中的裂纹;(c)Sn37Pb合金中的裂纹;(d)背铝层中的裂纹;(e)背铝层中的裂纹;(f)硅片中的裂纹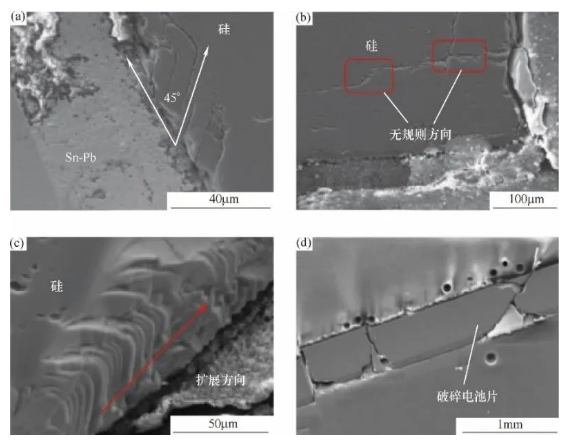
晶硅电池片中裂纹的扩展形貌
(a)单晶电池片中的裂纹;(b) 多晶电池片中的裂纹;(c) 裂纹的扩展轨迹;(d) 破碎的电池片
统计分析电磁感应焊接和红外加热焊接产生裂纹、虚焊电池片的数量,来衡量电磁感应的焊接质量。电磁感应加热技术对不同的材料具有不同的加热效率,不同的加热效率将引起材料间的温度差,继而产生内应力。但电磁感应焊接技术焊接质量良好,引起的缺陷占电池片总数的0.4%,裂纹电池片占据了缺陷电池片的66.7%。
无主栅双玻晶硅组件虚焊裂纹比例
对栅线焊接过程中,晶硅电池产生的裂纹情况进行分析统计得出:单晶硅比多晶硅电池更容易产生裂纹缺陷。相同的电磁感应焊接工艺,单晶电池中裂纹占缺陷总数的80.2%,斜裂纹是主要裂纹且占据比例为44.9%。多晶电池中裂纹占缺陷总数的59.4%,与主栅垂直的短裂纹是主要裂纹且占据比例为46.8%。此外,交叉裂纹在两种电池片中出现的频率也较高,在单晶硅和多晶硅电池片中分别占比为25.9%和17.6%。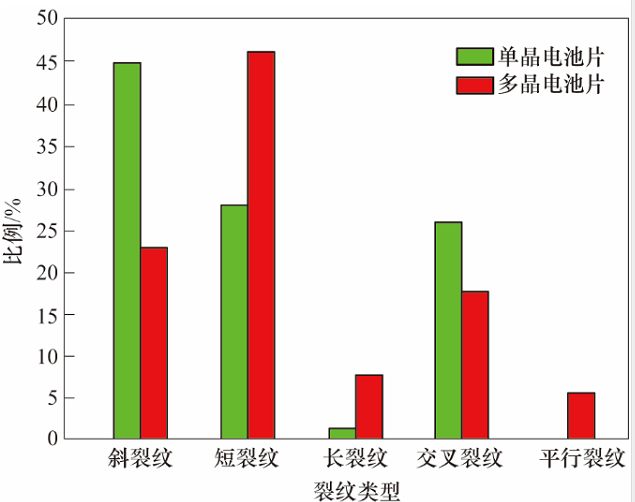
不同裂纹类型占总裂纹比例
对该组件的抗湿热老化能力、抗热循环老化能力进行测试得出:无主栅双玻组件的抗湿热老化能力优于无主栅单玻组件。在3000小时的湿热老化过程中,双玻组件输出功率衰减率稳定维持在每500小时0.07%~0.16%。而单玻组件输出功率衰减率最大时达到1.63%。并且,无主栅双玻组件的抗热循环老化能力也明显优于无主栅单玻组件。400次热循环老化过程,双玻组件输出功率的最终衰减率为4.41%,而单玻组件在227次热循环就已失效且其输出功率衰减率为10.75%。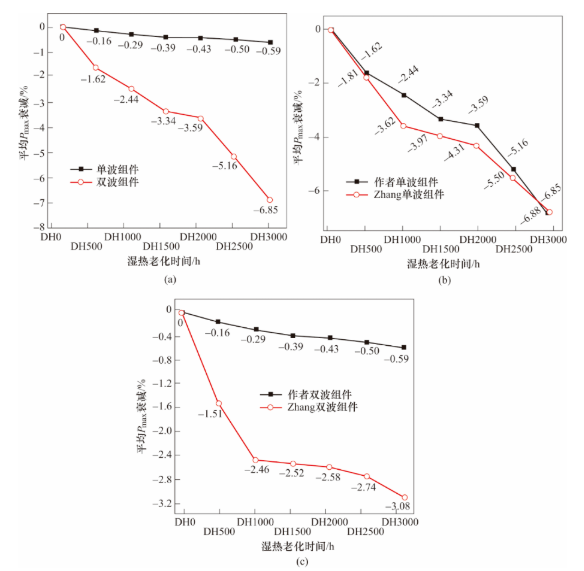
各实验组件在湿热老化过程的输出功率衰减曲线比较
(a)单玻组件和双玻组件;(b)不同单玻组件;(c)不同双玻组件较多学者研究了组件中电池片在湿热老化环境下的失效机理,但几乎都是关注电池片前表面而很少关注背面的失效特性。因此,对电池片背面和焊接处的失效特性分析和观察具有现实意义。首先对比电池片中背铝层、背面电极和焊接处在不同湿热环境下的腐蚀特性。研究发现,在不同环境下无主栅组件中电池片的失效机理不同。
湿热过程中多晶硅电池的腐蚀规律为:背铝层的腐蚀导致其结构变疏松及Al-Si共晶层变薄,并产生表面光滑的铝氧化物;背电极的腐蚀导致其表面变色并产生表面光滑的铝氧化物;焊接处的腐蚀最先发生于边缘部分且腐蚀区域沿着Ag电极和Sn37Pb合金间的界面向中心扩展。
背铝层在高乙酸浓度环境(25°C,85%湿度)处理前后的断面图
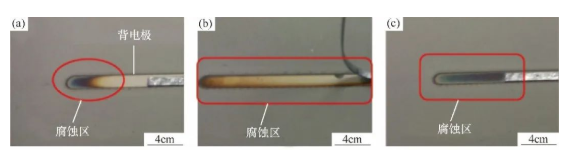
室温环境(25°C,45%湿度,0~2个月)处理后背电极不同变化情况
(a)背电极出现黄色和靛蓝色;(b)背电极出现黄色;(c)出现靛蓝色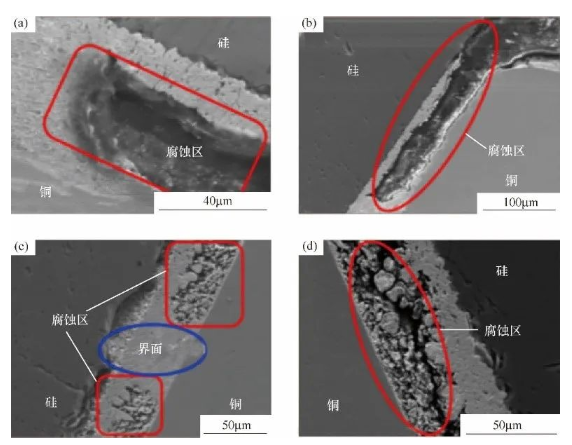
放置于高乙酸环境下(25°C,85%湿度)不同时间后焊接处微观结构图
(a)60h;(b)120h;(c)180h;(d)240h对无主栅组件的热循环过程中的失效形式进行分析,发现热循环过程中无主栅组件的主要失效形式是电池片两端虚焊。原因在于:热循环过程,温度变化引起不同材料在不断发生收缩和膨胀,这将在焊接处产生内应力从而导致疲劳破坏,由此使虚焊处恶化,最终焊条与电池片发生分离导致导电性能变差。热循环过程组件中电池片出现的三种虚焊类型
(a)焊条部脱落分脱离;(b)焊条脱落且无电连接;(c)焊条脱落但存在电连接
研究发现,具有高达35%的反射率存在于未进行表面处理的晶硅电池受光面,这导致大量的太阳光在受光面被反射,直接影响光生载流子的产生,从而降低晶硅电池的光电转换效率。在晶硅电池表面制备一层或多层具有一定光学性质的薄膜,即减反射膜(减反膜),可以增加透射进入晶硅电池内部的光子量,减少晶硅电池表面对光的反射损耗,提高晶硅电池光电转换效率。罗学涛、牛海燕团队就减少太阳光反射,设计出一款减反射膜双玻晶硅组件,具体如下:
针对降低EVA/晶硅电池界面间光反射损失,设计一种TiO2-SiO2/SiO2/SiNx多层减反膜层型双玻晶硅组件。经初步分析,此类型减反膜能够很好地与多晶硅基底结合。
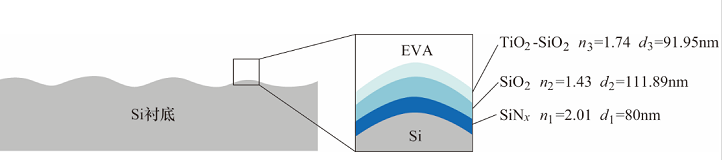
多层减反膜设计示意图

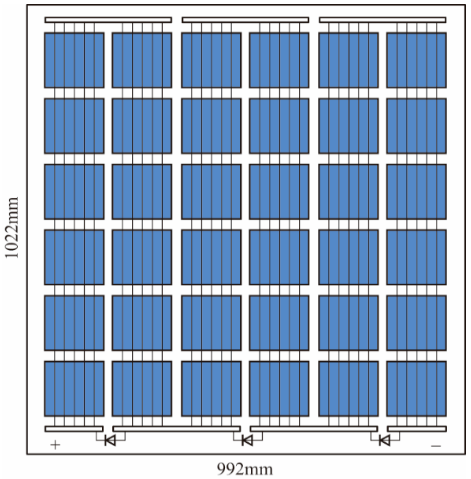
光伏组件结构示意图
02 TiO2-SiO2/SiO2/SiNx减反膜光学性能在220~1200nm的光波长范围内,采用TiO2-SiO2/SiO2/SiNx减反膜的光伏组件平均反射率低至7.67%,与采用SiNx和SiO2/SiNx减反膜的光伏组价平均反射率相比明显得到优化。在多晶硅电池的主要吸收光波长范围280~780nm范围内,采用TiO2-SiO2/SiO2/SiNx减反膜的光伏组件平均反射率低至6.54%,比采用SiNx和SiO2/SiNx减反膜的光伏组件反射率低了0.83%和0.49%。因此,SiNx、SiO2和TiO2-SiO2非常适合作为减反膜来降低晶硅电池的反射率,有利于构建高性能的太阳能晶硅电池。
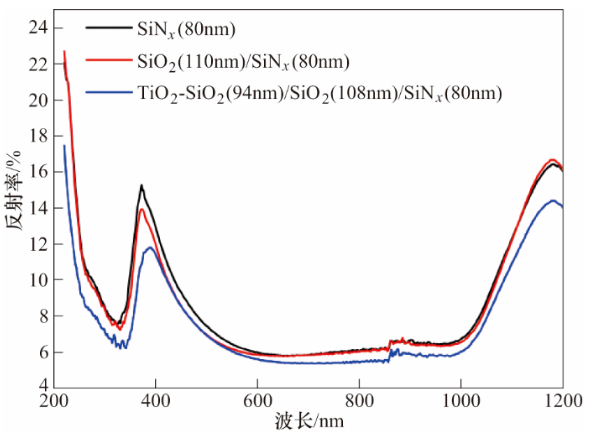
不同减反膜多晶硅电池封装反射率曲线
03 TiO2-SiO2/SiO2/SiNx减反膜组件的电学性能
采用TiO2-SiO2/SiO2/SiNx减反膜的光伏组件中,有88%的短路电流(Isc)大于9.20A。采用SiNx减反膜的光伏组件中,有72%的Isc≤9.15A,采用SiO2/SiNx减反膜的光伏组件,有72%位于9.15A<Isc≤9.20A。TiO2-SiO2/SiO2/SiNx减反膜的光伏组件短路电流(Isc)改善效果最好。
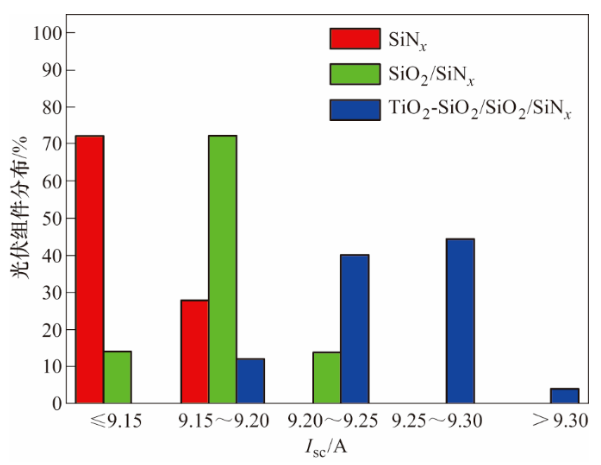
具有不同减反膜的光伏组件的短路电流分布情况
综合各项试验指标分析,TiO2-SiO2/SiO2/SiNx减反膜可以降低光伏组件中EVA与晶硅电池间界面的反射损耗,改善电路电流,使得光伏组件具有较高的转换效率。但采用TiO2-SiO2/SiO2/SiNx减反膜结构的光伏组件的平均填充系数改善不大,未来需对烧结和焊接工艺进一步优化。
未完待续:分片和贴膜双玻晶硅组件技术、N型双面半片双玻晶硅组件技术、叠瓦双玻晶硅组件技术、多主栅叠片双玻晶硅组件技术的总结概述……