海上油气进口和海洋油气产业作为我国海工装备制造业的重要组成部分,在双碳目标和国内油气消费增长的背景下得到快速发展,其生产、输送环境恶劣,在耐高压、-162℃超低温、耐腐蚀及耐候性等方面要求更高。而大口径厚壁不锈钢焊管因其具有高强度、高耐腐蚀性及良好的低温塑性,能克服极端温度、高压、腐蚀极端环境,是我国海上油气进口和开发不可或缺的基础管材。因此,市场对大口径不锈钢焊管需求急剧增加,且管材大量依靠进口,在交货期、技术性能、技术标准上均设置门槛,对我国相关行业形成壁垒。造成这种局面的原因有以下三个方面:
1、传统JCOE制备方式均应用于生产“黑材”,容易出现壁厚不均匀、开口度不一致、圆度不足等缺陷,严重的将出现不能修复而报废,目前大口径厚壁不锈钢焊管生产中间环节繁冗,良品率低,满足不了多品种、多规格产品连续化生产需求。2、大口径厚壁不锈钢焊管因生产技术不成熟,导致在服役过程中极易出现“跑”、“冒”、“滴”、“漏”等现象,产品性能难以满足极端环境需求,而油气输送管路对尺寸与低温韧性要求更加严格,因此重点开展关键技术研究是提升管材服役行为的重要手段。3、目前国内拥有的设备均是从国外进口或者国内单台设备按工序组成离散型产线,设备价格昂贵,缺少自主研发的经验与能力。因此需要结合大口径厚壁不锈钢焊管成形理论、工艺的研究,提出与产线需求一致的装备结构形式与生产能力,打破大口径厚壁不锈钢焊管装备依赖进口的现状。项目团队经过十多年的联合攻关,解决了成形与焊接的问题,在此基础上辅助制备工艺、热处理技术以及与之匹配的装备。构建弯曲成形、连续焊接协同加工体系,解决管体成形与焊接性能一致性的问题,融合合理的工艺制度、热处理技术以及与之匹配的装备,制备出满足市场需求的大口径厚壁不锈钢直缝焊管。其总体思路如图1所示。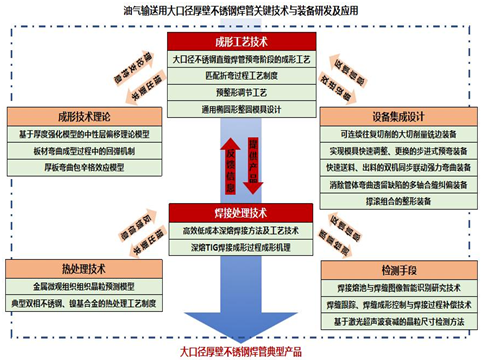
图1 大口径厚壁不锈钢焊管总体思路
创新点一、基于厚壁板材中性层偏移、弯曲回弹、包辛格效应理论,构建了获得板边预弯、管体连续折弯与精整成形方法,为工艺制定和装备研发提供了理论依据,形成不同规格产品单道次折弯过程中性层偏移量(板厚6%-18%)、回弹(板厚0.8%)等精准控制,解决了管体折弯成形过程尺寸偏差与缺陷难题。开展应力中性层与几何中心层偏移规律研究,构建基于厚度强化模型的中性层偏移方法,可辅助预测管体折弯过程每道次管壁减薄量以及管径延伸量,实现原始坯料精确定宽;开展板材弯曲成形过程回弹机制研究,构建可有效控制折弯角度的方法,回弹量平均值约为板厚的0.8%左右,实现了板坯折弯卸载后回弹量的精确预测,有效避免管体成形出现焊缝开口较大、周向圆度不良缺陷;开展板材弯曲过程加/卸载过程中包辛格效应研究,构建厚板弯曲包辛格效应方法,与实际测量误差小于10%,为厚壁不锈钢焊管JCOE成形工序中管体预弯、连续折弯成形工艺制定提供技术依据。
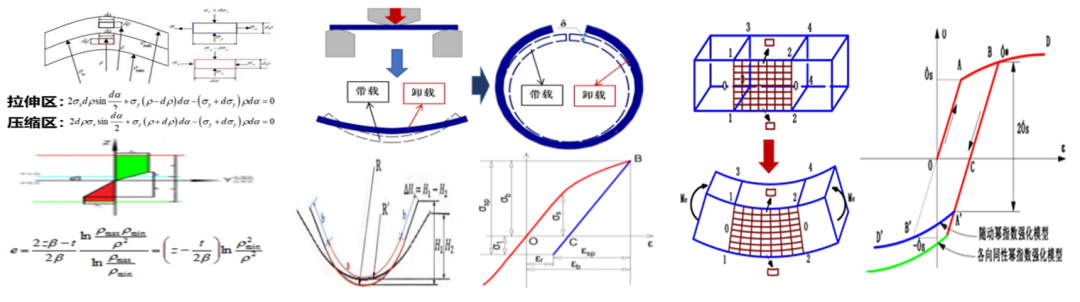
图2 厚壁板材中性层偏移、弯曲回弹、包辛格效应等方法
创新点二、研究了管体成形过程关键工序模具构型,揭示了不同材质、规格产品成形过程的变形规律,获得满足生产需求的成形工艺技术体系,解决了成形过程中产生缺陷等技术难题。开展预弯模具对大口径厚壁焊管在预弯阶段的影响规律研究,制定出满足大口径不锈钢直缝焊管预弯阶段的成形工艺。构建可满足不同直径、壁厚管材的板坯预弯成形凹凸模具,基于管坯直边弧边转变区域的预弯模具过渡段、上下模具相位差优化设计方法,板材厚度每增加10mm,过渡段角度增加1°,过渡段弯曲量增加9mm左右,有效实现下模行走行程与加载方式精准控制,实现了不同直径管体成形一模多用的效果;开展板材折弯成形过程步进式连续弯曲成形研究,优化了上模具压下量、下模具开口度及下压道次等工艺参数,折弯成形上模具压下量和下模开口度、折弯道次优化设计方法,提高了管体尺寸精度,满足不同规格管体生产的最优折弯成形工艺要求,实现了管体制备阶段高效化、精确化;开展预整形机多自由度合缝研究,优化了合缝辊位置、轴向压下角度的调节工艺,构建基于不同开口度预整形调整方法与关键技术、“桃形”“梨形”“错边”等特殊缺陷优化机理,实现了管体焊缝精准对接,提高管体成形质量。
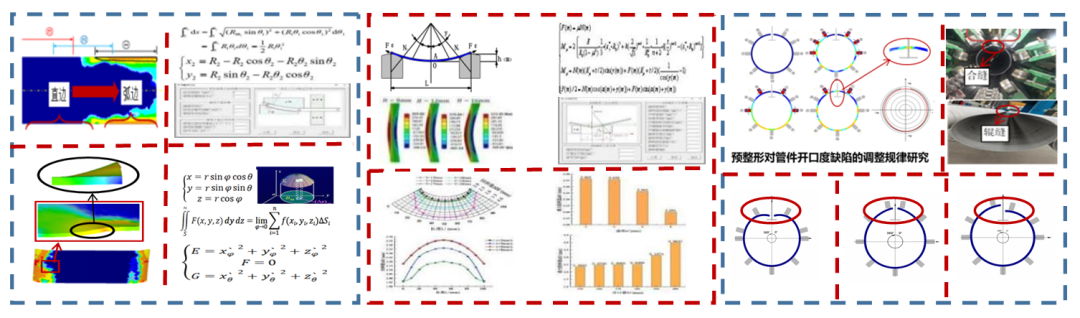
图3 管体成形过程关键工序模具构形设计方法与工艺调控技术
创新点三、开发了焊接熔池与焊缝图像智能识别跟踪、焊缝成形智能工艺控制技术、焊缝质量的全流程监控与动态优化技术,熔池形态识别正确率达96.34%,焊缝缺陷识别和检测准确率达95%以上,焊接成本降低30%以上,效率提高10倍。开发出满足大直径厚壁焊管焊接需求的高效低成本深熔焊接方法及工艺技术,开展深熔TIG焊接成形过程力学分析,利用热流固耦合进行深熔TIG焊接数值模拟,获得了深熔TIG焊接成形过程工艺;构建基于焊缝熔池及凝固成形后焊缝形状的捕捉系统,获得了焊接熔池与焊缝图像智能识别技术;开展基于视觉传感、电压电流多信息融合的熔池特征数据采集系统研究,掌握焊缝跟踪、焊缝成形控制与焊接过程补偿技术,熔池形态识别方面正确率达96.34%,准确率和检测效率达95%以上,获得焊接过程焊缝成形质量智能控制,准确的预测熔池力学行为及熔宽形貌,确保了厚壁焊管焊缝质量与基体不锈钢材料的性能一致性,提高焊接质量及焊接效率。
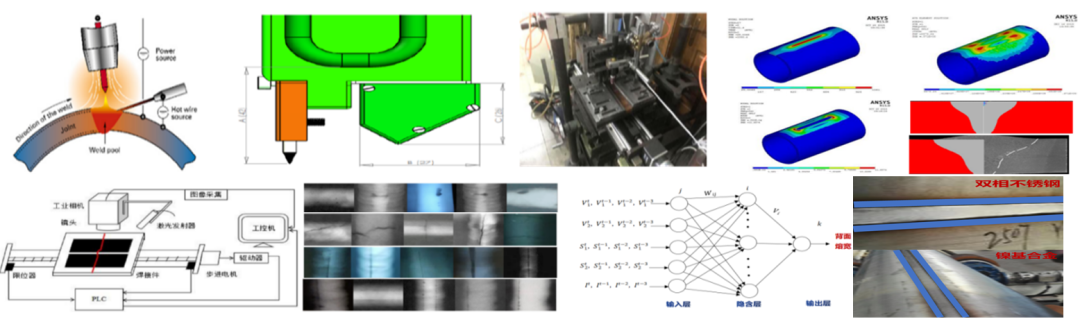
图4 管体厚壁不锈钢焊管图像动态识别、智能补偿的高效焊接方法
创新点四、开发了可实现焊缝与母材性能一致性调控、晶粒尺寸在线检测方法等关键技术,实现了管材热处理过程组织性能与析出相的动态调控,在线晶粒度误差小于10%,解决了晶粒度预测难、焊缝开裂、焊接部分与基体性能一致性差等难题。构建了微观组织晶粒预测方法,发现了管材在不同温度下的组织晶粒的再结晶、晶粒长大等变化规律,实现了晶粒度精确控制;建立激光超声波衰减的晶粒尺寸检测方法,实现了管材微观晶粒尺寸的在线实时检测;基于成形后的管材需进行热处理行为实现管件焊缝与母材组织与性能的一致性,研究双相不锈钢、镍基合金相变规则,阐明在不同温度条件下的相变特征,构建可实现焊缝和基体性能一致性的关键技术,结合CCT及TTT曲线,避免无效及有害温度,形成典型双相不锈钢、镍基合金的热处理工艺制度。
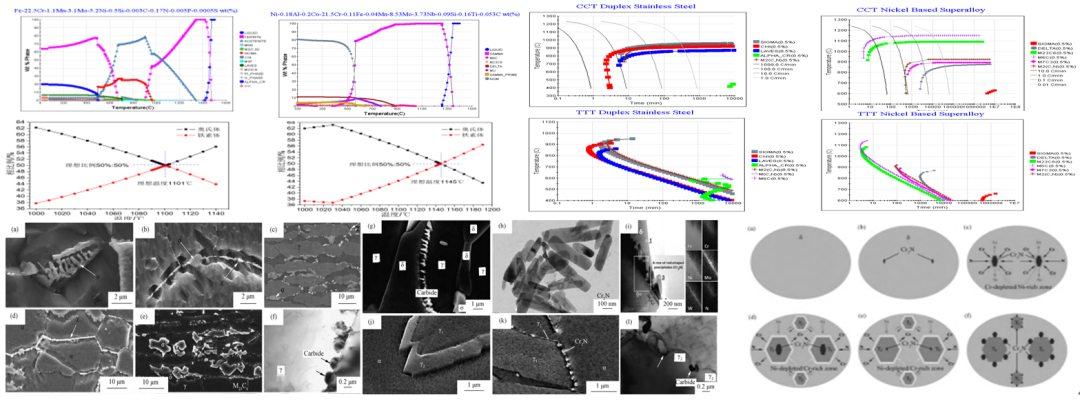
图5 厚壁不锈钢焊管热处理过程组织晶粒、析出相等演变机理
创新点五、研制出大口径厚壁不锈钢焊管成套装备,构建了非对称布置的板边预弯、管体连续折弯等关键结构形式,实现了工艺与设备的集成创新,形成Φ219-Φ1219mm、壁厚80mm、长度12500mm系列产品生产技术,效率提高2倍以上。发明出可连续往复切削的大切削量铣边装备,构建快速响应厚壁焊管焊缝倒角大切削量需求的多刀头切削方式与快速定宽、定厚、刀头角度调整的结构形式,生产效率提升2倍以上;发明出厚壁焊管板边预弯需求的错边非对称布置形式与多曲面弧段组合大步长弯曲方式,可实现模具快速调整、更换的步进式预弯,预弯边2800mm以上、模具投资为传统预弯装置的40%;构建了厚壁焊管管体弯曲需求的高刚度“C”形结构布置形式与大跨度双机组合连续折弯设备结构形式,发明出快速送料、出料的双机同步联动的强力弯曲装备,机组能力2×3000t、同步精度达到±0.1mm;发明出厚壁焊管管体多自由度合缝结构形式、消除管体弯曲成形过程遗留缺陷的多轴合缝纠偏装备,实现智能焊接降低人为因素、调速范围为0.2m/s-0.7m/s。
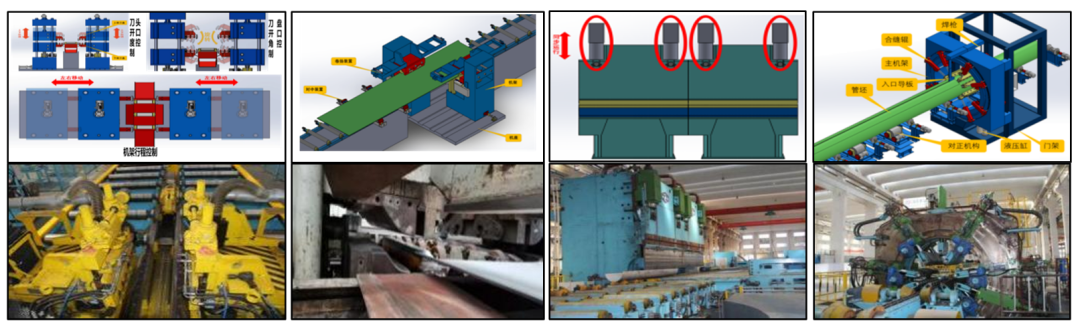
图6 大口径厚壁不锈钢焊管高质高效制备的成套装备
项目在国家973计划、国家自然科学基金、山西省重大专项、国家火炬计划产业化示范项目等重大专项的支撑下,通过十多年联合技术攻关,发明了经济高效的JCOE连续制管工艺的专有技术,拥有全部自主知识产权的首条大口径厚壁不锈钢焊管装备,满足柔性生产的多规格、多品种的要求。系列产品整体达到芬兰Outokumpu、韩国EEW公司、德国Butting同类产品水平,部分指标优于国外水平。本项目已获专利59件(发明专利30件),软件著作权11件,论文59篇,起草了国家标准16项。产品已应用于“一带一路”俄罗斯亚马尔LNG2液化天然气项目、阿尔及利亚国家石油公司Kurvers Piping高硫原油输送管线项目、伊拉克哈法亚CPF3项目以及山东LNG接收站、广西LNG接收站、天津LNG接收站、浙江石化的4000万吨/年炼化一体化项目等230多项大中型工程项目,累计销售近10万吨,实现销售24亿元,利税4.55亿元,提升我国不锈钢焊管产业整体竞争力,对提升高端装备制造水平及国产化率有较大现实意义。